漸開線圓柱齒輪承載能力計算方法
1 范圍
本標準適用于鋼、鑄鐵制造的,基本齒廓符合GB 1356—87 的內(nèi)、外嚙合直齒、斜齒和人字齒(雙斜齒)圓柱齒輪傳動;君X廓與GB 1356—87 相類似,但個別齒形參數(shù)值略有差異的齒輪,亦可參照本標準計算其承載能力。
本標準包括齒面接觸強度和輪齒彎曲強度兩種校核計算方法。
本標準規(guī)定相對應的齒輪精度標準為GB 10095—88 。對于采用其它精度標準的齒輪,當采用本標準的簡化方法計算有關載荷系數(shù)時,應折算成規(guī)定標準的相應精度等級。
本標準是各部門和行業(yè)制定齒輪承載能力計算標準和規(guī)范的基礎。
2 引用標準
下列標準所包含的條文,通過在本標準中引用而構成為本標準的條文。本標準出版時,所示版本均為有效。所有標準都會被修訂,使用本標準的各方應探討使用下列標準最新版本的可能性。
GB 1356—87 漸開線圓柱齒輪 基本齒廓
GB/T 3374—92 齒輪基本術語
GB 8539—87 齒輪材料熱處理質量檢驗的一般規(guī)定
GB10095—88 漸開線圓柱齒輪精度
3 概述
3.1 可靠性與安全系數(shù)
不同的使用場合對齒輪有不同的可靠度要求。齒輪工作的可靠性要求是根據(jù)其重要程度、工作要求和維修易等方面的因素綜合考慮決定的。一般可分為下述幾類情況:
a) 低可靠度要求 齒輪設計壽命不長,對可靠度要求不高的易于更換的不重要齒輪,或齒輪設計壽命雖不短,但對可靠性要求不高。這類齒輪可靠度可取為90%。
b) 一般可靠度要求 通用齒輪和多數(shù)的工業(yè)應用齒輪,其設計壽命和可靠性均有一定要求。這類齒輪工作可靠度一般不大于99%。
c) 較高可靠度要求 要求長期連續(xù)運轉和較長的維修間隔,或設計壽命雖不很長時間但可靠性要求較高的高參數(shù)齒輪,一旦失效可能造成較嚴重的經(jīng)濟損失或安全事故,其可靠要求甚至高達99.9%。
d) 高可靠度要求 特殊工作條件下要求可靠度很高的齒輪,其可靠度要求甚至高達99.99%以上。
目前,可靠性理論雖已開始用于一些機械設計,且已表明只用強度安全系數(shù)并不能完全反映可靠性水平,但是在齒輪設計中將各參數(shù)作為隨機變量處理尚缺乏足夠數(shù)據(jù)。所以,本標準仍將設計參數(shù)作為確定值處理,仍然用強度安全系數(shù)或許用應力作為判據(jù),而通過選取適當?shù)陌踩禂?shù)來近似控制傳動裝置的工作可靠度要求。考慮到計算結果和實際情況有一定偏差,為保證所要求的可靠性,必須使計算允許的承載能力有必要的安全裕量。顯然,所取的原始數(shù)據(jù)越準確,計算方法越精確,計算結果與實際情況偏差就越小,所需的安全裕量就可以越小,經(jīng)濟性和可靠性就更加統(tǒng)一。
具體選擇安全系數(shù)時,需注意以下幾點:
a) 本標準所推薦的齒輪材料疲勞極限(見8.1)是在失效概率為1%時得到的。可靠度要求高時,安全系數(shù)應取大些;反之,則可取小些。
b) 一般情況下彎曲安全系數(shù)應大于接觸安全系數(shù),同時斷齒比點蝕的后果更為嚴重,也要求彎曲強度的安全裕量應大于接觸強度安全裕量。
c) 不同的設計方法推薦的最小安全系數(shù)不盡相同,設計者應根據(jù)實際使用經(jīng)驗或適合的數(shù)據(jù)選定。無可用數(shù)據(jù)時,可參考附錄A(標準的附錄)選取。
d) 對特定工作條件下可靠度要求較高的齒輪安全系數(shù)取值,設計者應作詳細分析,并且通常應由設計制造部門與用戶商定。
3.2 主要代號
本標準的主要代號及其意義和單位見表1 。
表1 主要代號
代 號 |
意 義 |
單 位 |
a
a′ |
中心距,標準齒輪及高度變位齒輪的中心距
角度變位齒輪的中心距 |
mm
mm |
b
bcal |
齒寬
計算齒寬 |
mm
mm |
C
Ca
Cay
cγ
c′ |
節(jié)點:系數(shù)
齒頂修緣量
由跑合產(chǎn)生的齒頂修緣量
輪齒單位齒寬總剛度平均值(嚙合剛度)
一對輪齒的單位齒寬的最大剛度(單對齒剛度) |
μm
μm
N/(mm·μm)
N/(mm·μm) |
d
d1,d2
da1,da2
db1,db2
df1,df2 |
直徑
小輪、大輪的分度圓直徑
小輪、大輪的齒頂圓直徑
小輪、大輪的基圓直徑
小輪、大輪的齒根直徑 |
mm
mm
mm
mm
mm |
E
e |
彈性模量(楊氏模量)
輔助量 |
N/mm2 |
Fbn
Fbt
Ft
Fβ
Fβx
Fβy
ff
fpb |
法面內(nèi)基圓周上的名義切向力
端面內(nèi)基圓周上的名義切向力
端面內(nèi)分度圓周上的名義切向力
齒向公差
初始嚙合齒向誤差
跑合后的嚙合齒向誤差
齒形公差
基節(jié)極限偏差 |
N
N
N
μm
μm
μm
μm
μm |
G |
切變模量 |
N/mm2 |
HB
HRC
HV1
HV10
h
hFa
hFe
ha
haP,hfP |
布氏硬度
洛氏硬度
F=9.8N時的維氏硬度
F=98.1N時的維氏硬度
齒高
載荷作用于齒頂時的彎曲力臂
載荷作用于單對齒嚙合區(qū)外界點時的彎曲力臂
齒頂高
刀具基本齒廓齒頂高和齒根高 |
mm
mm
mm
mm
mm |
KA
KFα
KFβ
KHα
KHβ
KV |
使用系數(shù)
彎曲強度計算的齒間載荷分配系數(shù)
彎曲強度計算的齒間載荷分配系數(shù)
接觸強度計算的齒間載荷分配系數(shù)
接觸強度計算的齒間載荷分配系數(shù)
動載系數(shù) |
|
L |
長度 |
mm |
M
m
mn
mred
mt |
彎矩
模數(shù);當量品質
法向模數(shù)
誘導品質
端面模數(shù) |
N·m
mm; kg/mm
mm
kg/mm
mm |
K
NL
n1,n2
nE1 |
臨界轉速比;指數(shù)
應力循環(huán)次數(shù)
小輪、大輪的轉速
小輪的臨界轉速 |
r/min
r/min |
P
Pbn
Pbt |
功率
法向基節(jié)
端面基節(jié) |
kW
mm
mm |
q
qs |
輔助系數(shù)
單位齒寬柔度
齒根圓角參數(shù) |
μm·mm/N |
Ra
Rz
r |
輪廓表面算術平均偏差
表面微觀不平度10點高度
半徑,分度圓半徑 |
μm
μm
mm |
SF
SF min
SH
SH min
s
sFn |
彎曲強度的計算安全系數(shù)
彎曲強度的最小安全系數(shù)
接觸強度的計算安全系數(shù)
接觸強度的最小安全系數(shù)
齒厚;尺寸
危險截面上的齒厚 |
mm
mm |
T1,T2 |
小輪、大輪的名義轉矩 |
N·m |
u |
齒數(shù)比u=z2/z1>1 |
|
v
wm
wmax
x1,x2 |
線速度,分度圓圓周速度
單位齒寬平均載荷
單位齒寬最大載荷
小輪、大輪的法向變位系數(shù) |
m/s
N/mm
N/mm
|
YF
YFa
YNT
YR rel T
YS
YSa
YST
YX
Yβ
Yδ rel T
Yε
yα
yβ |
載荷作用于單對齒嚙合區(qū)外界點時的齒形系數(shù)
載荷作用于齒頂時齒表系數(shù)
彎曲強度計算的壽命系數(shù)
相對齒根表面狀況系數(shù)
載荷作用于單對齒嚙合區(qū)外界點時的應力修正系數(shù)
載荷作用于齒頂時的應力修正系數(shù)
試驗齒輪的應力修正系數(shù)
彎曲強度計算的尺寸系數(shù)
彎曲強度計算的螺旋角系數(shù)
相對齒根圓角敏感系數(shù)
彎曲強度計算的重合度系數(shù)
齒廓跑合量
齒向跑合量 |
μm
μm |
ZB,ZD
ZE
ZR
ZL
ZNT
ZR
ZV
ZW
ZX
Zβ
Zε
z1,z2
zn |
小輪,大輪單對齒嚙合系數(shù)
彈性系數(shù)
節(jié)點區(qū)域系數(shù)
潤滑劑系數(shù)
接觸強度計算的壽命系數(shù)
粗糙度系數(shù)
速度系數(shù)
齒面工作硬化系數(shù)
接觸強度計算的尺寸系數(shù)
接觸強度計算的螺旋角系數(shù)
接觸強度計算的重合度系數(shù)
小輪、大輪的齒數(shù)
斜齒輪的當量齒數(shù) |
|
αFan
αFat
αFen
αFet
αan
αat
αen
αet
αn
αt
αt′ |
齒頂法向載荷作用角
齒頂端面載荷作用角
單對齒嚙合區(qū)外界點處法向載荷作用角
單對齒嚙合區(qū)外界點處端面載荷作用角
齒頂法向壓力角
齒頂端面壓力角
單對齒嚙合外界點處的法向壓力角
單對齒嚙合外界點處的端面壓力角
法向分度圓壓力角
端面分度圓壓力角
端面分度圓嚙合角 |
°,rad
°,rad
°,rad
°,rad
°,rad
°,rad
°,rad
°,rad
°,rad
°,rad
°,rad |
β
βb
βe |
分度圓螺旋角
基圓螺旋角
單對齒嚙合區(qū)外界點處螺旋角 |
°,rad
°,rad
°,rad |
γ |
輔助角 |
°,rad |
εα
εβ
εγ |
端面重合度
縱向重合度
總重合度 |
|
1,2 |
小輪、大輪的轉動慣量 |
kg·mm2 |
υ |
潤滑油運動粘度
泊桑比 |
mm2/s(eSt)
|
ρ
ρfP
ρF |
密度
基本齒條齒根過渡圓角半徑
危險截面處齒根圓角半徑 |
kg/mm2
mm
mm |
σb
σF
σFo
σFP
σF lim
σH
σHo
σHP
σH lim |
抗拉伸強度
計算齒根應力
計算齒根應力基本值
許用齒根應力
試驗齒輪的彎曲疲勞極限
計算接觸應力
計算接觸應力基本負
許用接觸應力
試驗齒輪的接觸疲勞極限 |
N/mm2
N/mm2
N/mm2
N/mm2
N/mm2
N/mm2
N/mm2
N/mm2
N/mm2 |
3.3 系數(shù)的分類和計算順序
本標準中涉及的影響系數(shù)就其對象來說有修正載荷、修正計算應力和修正許用應力三大部分。這些系數(shù)可分為兩類:
a)由幾何關系或常規(guī)方法確定的系數(shù),如修正計算應力的系數(shù)。這些系數(shù)按標準提供的公式計算確定。
b)受多種因素影響但被獨立處理的系數(shù)。這些因素雖然在一定程度上是相關的,但目前尚難作精確的定量計算。例如,修正載荷的系數(shù)KA,KV,KHβ(KFβ),KHα,(KFα)以及修正許用應力的諸系數(shù)。
對于修正載荷的諸系數(shù),最理想的方法是通過精密實測或對傳動系統(tǒng)作全面的力學分析得到,也可從大量的現(xiàn)場經(jīng)驗確定。這時,應對所采用方法的精確度和可靠性加以認證,并要明確其前提條件。
當由于技術或經(jīng)濟上的原因使上述方法難以實現(xiàn)時,可選取本標準提供的兩種方法(即一般方法和簡化方法)之一來確定KV,KHβ(KFβ)和KHα,(KFα)。簡化方法主要用于總體方案設計和非重要齒輪的核算。在對計算結果有爭議時,以一般方法為準。對于要求計算精確度較高的齒輪,各系數(shù)應優(yōu)先采用一般方法或更精確的其它方法計算。
各修正載荷的系數(shù)與其相應的端面內(nèi)分度圓上切向力有關,需按以下順序計算:
a)用FtKA求KV;
b)用FtKAKV求KHβ(KFβ);
c)用FtKAKVKHβ求KHα(KFα);
對于修正許用應力的諸系數(shù),本標準對每個系數(shù)的諸影響因素均按獨立變量處理;在取值上除個別某些系數(shù)(如三個潤滑油膜影響系數(shù)ZL,ZV,ZR)外,均只提供一個公式或經(jīng)驗數(shù)據(jù)。
4 某計算公式
4.1 齒面接觸強度核算
本標準把赫茲應力作為齒面接觸應力的計算基礎,并用來評價接觸強度。赫茲應力是齒面間應力的主要指標,但不是產(chǎn)生點蝕的唯一原因。例如在應力計算中未考慮滑動的大小和方向、摩擦系數(shù)及潤滑狀態(tài)等,這些都會影響齒面的實際接觸應力。
齒面接觸強度核算時,取節(jié)點和單對齒嚙合區(qū)內(nèi)界點接觸應力中的較大值,小輪和大輪的許用接觸應力σHP 要分別計算。下列公式適用于端面重合度εα<2.5的齒輪副。
在任何嚙合瞬間,大、小齒輪的接觸應力總是相等的。分析計算表明,齒面最大接觸應力一般出現(xiàn)在小輪單對齒嚙合區(qū)內(nèi)界點B、節(jié)點C及大輪單對齒嚙合區(qū)內(nèi)界點D這三個特征點之一處上(B、C、D三點可參見圖12)。實際使用和實驗均表明,由于上述除赫茲應力外的其它因素影響,產(chǎn)生點蝕的危險的實際接觸應力通常出現(xiàn)在C、D點或其間(對大齒輪),或在C、B點或其間(對小齒輪)1]。式(5)是基于節(jié)點區(qū)域系數(shù)ZH計算得節(jié)點C處接觸應力基本值σHO,當單對齒嚙合區(qū)內(nèi)界點處的應力超過節(jié)點處的應力時,即ZB或ZD大于1.0時,在確定大、小齒輪計算應力σH時應乘以ZD,ZB予以修正;當ZB或ZD不大于1.0時,取其值為1.0。
對于斜齒輪,當縱向重合度εβ≥1時,一般地節(jié)點接觸應力較大;當縱向重合度εβ<1時,接觸應力由與斜齒輪齒數(shù)相同的直齒輪的σH和εβ=1的斜齒輪的σH按εβ作線性插值確定。
4.1.1 強度條件
大、小輪在節(jié)點和單對齒嚙合區(qū)內(nèi)界點處的計算接觸應力中的較大值σH,均應不大于其相應的許用接觸應力σHP ,即:
σH≤σHP………………………………………………(1)
或接觸強度的計算安全系數(shù)SH均應不大于其相應的最小安全系數(shù)SH min ,即
SH≥SH min………………………………………………(2)
上述兩式中:σH——齒輪的計算接觸應力,N/min2,見4.1.2;
σHP——齒輪的許用接觸應力,N/min2,見4.1.3;
SH——接觸強度的計算安全系數(shù),見4.1.4;
SH min——接觸強度的最小安全系數(shù),見3.1及附錄A。
4.1.2 計算接觸應力σH
小輪和大輪的計算接觸應力σH1,σH2分別按下述兩式確定:
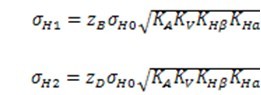
上述兩式中:K
A——使用系數(shù),見6.1;
KV——動載系數(shù),見6.2;
KHβ——接觸強度計算的齒向載荷分布系數(shù),見6.3;
KHα——接觸強度計算的齒間載荷分配系數(shù),見6.4;
ZB,ZD——小輪及大輪單對嚙合系數(shù),見7.1.5;
σH0——節(jié)點處計算接觸應力的基本值,N/min2,用下式計算:
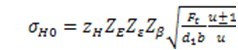
……………………………………(5)
式中:Ft——端面內(nèi)分度圓上的名義切向力,N,見第5章;
B——工作齒寬,mm,指一對齒輪中的較小齒寬;
d1——小齒輪分度圓直徑,mm;
u——齒數(shù)比,u=z2/z1,z1,z2分別為小輪和大輪的齒數(shù);
ZH——節(jié)點區(qū)域系數(shù),見7.1.1;
Z
E——彈性系數(shù),
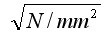
,見7.1.2;
Zε——重合度系數(shù),見7.1.3;
Zβ——螺旋角系數(shù),見7.1.4。
式(5)中的“+”號用于外嚙合傳動;“-”號用于內(nèi)嚙合傳動。
4.1.3 許用接觸應力σHP
4.1.3.1 一般方法
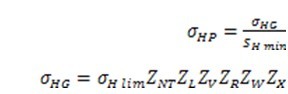
式中:σ
HP——計算齒輪的接觸極限應力,N/mm
2;
σH lim——試驗齒輪的接觸疲勞極限,N/mm2,見8.1;
ZNT——接觸強度計算的壽命系數(shù),見8.2.1;
ZL——潤滑劑系數(shù),見8.3.1;
ZV——速度系數(shù),見8.3.1;
ZR——粗糙度系數(shù),見8.3.1;
ZW——工作硬化系數(shù),見8.4;
ZX——接觸強度計算的尺寸系數(shù),見8.5.1 。
4.1.3.2 簡化方法
由式(7)計算σHG時,系數(shù)ZL,ZV,ZW按簡化方式確定。
4.1.4 接觸強度的計算安全系數(shù)SH

……………………………………..(8)
式中的各參數(shù)對一般方法和簡化方法應分別確定。大、小輪的SH應分別計算。不同使用場合對安全系數(shù)的考慮參見3.1,σHG和σH計算分別按式(7)和式(3)。
4.2 輪齒彎曲強度核算
作為判斷的齒根應力,原則上可用任何適宜的方法(如有限元法、積分法、保角變換法)或實際測量(如光彈測量、應變測量)來確定。在考慮了同時嚙合的各對輪齒間載荷分配后,用上述方法之一來確定產(chǎn)生最大齒根應力的載荷作用位置及其相應的最大齒根應力是較理想的方法。
本標準以載荷作用側的齒廓根部的最大拉應力作為名義彎曲應力,并經(jīng)相應的系數(shù)修正后作為計算齒根應力。
考慮到使用條件、要求及尺寸的不同,本標準將修正后的試件彎曲疲勞極限作為齒根應力。
本標準的輪齒彎曲強度計算式適用于齒根以內(nèi)輪緣厚度不小于3.5mn的圓柱齒輪。對于不符合前述條件的薄輪緣齒輪,應作進一步應力分析、實驗或根據(jù)經(jīng)驗資料確定其齒根應力的增大率。在無法采用上述方法時,可參考附錄C近似確定2] 。
4.2.1 強度條件
計算齒根應力σF 應不大于許用齒根應力σFP,即:
σF≤σFP……………………………………..(9)
或彎曲強度的計算安全系數(shù)SF應不小于彎曲強度的最小安全系數(shù)SF min ,即
SF≥SF min……………………………………(10)
上述兩式中:σF——齒輪的計算齒根應力,N/mm2,見4.2.2;
σFP——齒輪的許用齒根應力,N/mm2,見4.2.3;
SF——彎曲強度的計算安全系數(shù),見4.2.4;
SF min——彎曲強度的最小安全系數(shù),見3.1及附錄A。
4.2.2 計算齒根應力σF
計算齒根應力σF由下式確定:
σF=σF0 KAKV KFβKFα……………………………………(11)
式中:KA,KV——見4.1.2說明;
KFβ——彎曲強度計算的齒向載荷分布系數(shù),見6.3.4;
KFα——彎曲強度計算的齒間載荷分配系數(shù),見6.4;
σF0——齒根應力的基本值,N/mm2,對于大、小齒輪應分別確定。
本標準提供下列兩種確定齒根應力基本值σF0的計算方法。對于計算精度要求較高的齒輪,應優(yōu)先采用方法一。在對計算結果有爭議時,以方法一為準。
a)方法一:本法是以載荷作用于單對齒嚙合區(qū)外界點為基礎進行計算的1)。齒根應力基本值可按下式確定:

…………………………………..(12)
式中:Ft——端面內(nèi)分度圓上的名義切向力,N;
b——工作齒寬(齒根圓處),mm。若大、小齒輪寬度不同時,最多把窄齒輪的齒寬加上一個模數(shù)作為寬齒輪的工作齒寬;對于雙斜齒或人字齒輪b=bB×2,bB為單個斜齒輪寬度;輪齒如有齒端修薄或鼓形修整,b應取比實際齒寬較小的值;
mn——法向模數(shù),mm;
YF——載荷作用于單對齒嚙合區(qū)外界點時的齒形系數(shù),見7.2.1;
YS——載荷作用于單對齒嚙合區(qū)外界點時的應力修正系數(shù),見7.2.2;
Yβ——螺旋角系數(shù),見7.2.4 。
b)方法二:本法是以載荷作用于齒頂為基礎進行計算的,僅適用于εα<2的齒輪傳動。齒根應力基本值按下式確定:
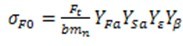
…………………………………..(13)
式中:YFα——載荷作用于齒頂時的齒形系數(shù),見7.2.1;
YSα——載荷作用于齒頂時的應力修正系數(shù),見7.2.2;
Yε——彎曲強度計算的重合度系數(shù),見7.2.3。
Ft,b,mn和Yβ的意義同式(12)的說明。
4.2.3 許用齒根應力σFP
大、小齒輪的許用齒根應力要分別確定。在采用以試驗齒輪的強度為依據(jù)所得到的數(shù)據(jù)時,其許用齒根應力可按下式確定2):
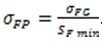
…………………………………..(14)

………………………………..(15)
式中:σFG ——計算齒輪的彎曲極限應力,N/mm2;
σF lim——試驗齒輪的齒根彎曲疲勞極限,N/mm2,見8.1.3;
YST—— 試驗齒輪的應力修正系數(shù),如用本標準所給σF lim值計算時,取
YST=2.0…………………………(16)
YNT——彎曲強度計算的壽命系數(shù),見8.2.2;
SF min——彎曲強度的最小安全系數(shù),見3.1及附錄A;
Yδrel T——相對齒根圓角敏感系數(shù),見8.6;
YRrel T——相對齒根表面狀況系數(shù),見8.7;
YX——彎曲強度計算的尺寸系數(shù),見8.5.2 。
4.2.4 彎曲強度的計算安全系數(shù)SF

………….………………………..(17)
式中符號的說明見4.2.2及4.2.3 , 大小齒輪的安全系數(shù)應分別計算。不同使用場合對安全系數(shù)的考慮參見3.1,σFG和σF計算分別按式(15)和式(11)。
5 名義切向力Ft
一般齒輪傳動的名義切向力由齒輪傳遞的名義功率或轉矩確定。名義切向力作用于端面內(nèi)并切于分度圓,可按下式計算:

………….………………………..(18)
式中:Ft——名義切向力,N;
d——齒輪分度圓直徑,mm;
T——名義轉矩,N·m。
當傳遞的名義功率P以kw計時,
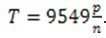
………….………………………..(19)
當傳遞的名義功率P以PS計時,
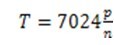
………….………………………..(20)
n——齒輪傳遞,r/min.
在變動載荷下工作的齒輪載荷、應力及其強度安全系數(shù)的核算,當缺乏更精確和更可靠的方法及數(shù)據(jù)可用時,可參考附錄B進行核算。
6 修正載荷的系數(shù)和輪齒剛度
6.1 使用系數(shù)KA
使用系數(shù)KA是考慮由于齒輪嚙合外部因素引起附加動載荷影響的系數(shù)。這種外部附加動載荷取決于原動機和從動機的特征,軸和聯(lián)軸器系統(tǒng)的質量和剛度以及運行狀態(tài)。
如有可能,使用系數(shù)應通過精密測量或對傳動系統(tǒng)的全面分析來確定。當上述方法不有實現(xiàn)時,可參考表2查收,但需注意以下幾點:
a)表2主要適用于在非共振區(qū)運行的工業(yè)齒輪和高速齒輪,采用表薦值時至少應取最小彎曲強度安全系數(shù)3]SF min=1.25
b)某些應用場合的使用系數(shù)KA值可能遠高于表2中示值(甚至高達10),選用時應認真并盡可能全面地分析工況和聯(lián)接結構。如在運行中存在非正常的重載、大的起動轉矩、重復的中等或嚴重沖擊,應當核算其有限壽命下承載能力和靜強度。
表2 使用系數(shù)KA
原動機工作特性 |
工 作 機 工 作 特 性 |
均勻平穩(wěn) |
輕微沖擊 |
中等沖擊 |
嚴重沖擊 |
均勻平穩(wěn) |
1.00 |
1.25 |
1.50 |
1.75 |
輕微沖擊 |
1.00 |
1.35 |
1.60 |
1.85 |
中等沖擊 |
1.25 |
1.50 |
1.75 |
2.0 |
嚴重沖擊 |
1.50 |
1.75 |
2.0 |
2.25或更大 |
注
1 對于增速傳動,根據(jù)經(jīng)驗建議取上表值的1.1倍。
2 當外部機械與齒輪裝置之間撓性聯(lián)接時,通常KA值可適當減小。 |
6.2 動載系數(shù)KV
動載系數(shù)KV是考慮齒輪制造精度、運轉速度對輪齒內(nèi)部附加動載荷影響的系數(shù),定義為:
K
V=

影響動載系數(shù)的主要因素有:
a)由基節(jié)和齒形誤差產(chǎn)生的傳動誤差;
b)節(jié)線速度;
c)轉動件的慣量和剛度;
d)輪齒載荷;
e)輪齒嚙合剛度在嚙合循環(huán)中的變化。
其他的影響因素還有:跑合效果、潤滑油特性、軸承及箱體支承剛度以及動平衡精度等。
如能通過實測或對所有影響因素作全面的動力學分析來確定包括內(nèi)部動載荷在內(nèi)的最大切向載荷,則可取KV等于1;但此時需對所采用方法的精度和可靠性加以論證,并明確給出前提條件。
在上述的要求難以實現(xiàn)時,可用本標準提供的下述方法之一計算動載系數(shù)。該方法的力學模型為:將大小齒輪的質量轉化到嚙合線上,并由彈簧聯(lián)結所形成的彈性振動系統(tǒng)。彈簧的剛度即為輪齒嚙合剛度。嚙合中的阻尼取為一個名義平均值,忽略滯后現(xiàn)象和軸承、聯(lián)軸器等附加阻尼因素。也忽略了軸、軸承和箱體變形的影響。由于未考慮上述各種附加阻尼,除在主共振區(qū)外,按本法求得的KV值通常比實際的略大一些。
6.2.1 一般方法
確定KV的計算式列于6.2.1.2中,為了使用這些公式,需首先確定臨界轉速比N。
6.2.1.1 臨界轉速比N
簡化了的齒輪嚙合振動模型存在一個臨界轉速nE1 ,小齒輪的運行轉速n1與臨界轉速nE1的比值N稱為臨界轉速比,即

………….………………………..(21)
臨界轉速nE1可按(22)計算
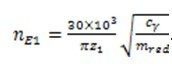
………….………………………..(22)
式中:nE1——小齒輪臨界轉速,r/min;
z1——小齒輪齒數(shù);
Cγ——輪齒嚙合剛度,N/(mm·μm),見6.5.2;
mred——誘導質量,kg/mm。
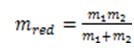
………….………………………..(23)
其中m1 ,m2分別表示小輪及大輪化到嚙合線上的單位齒寬當量質量,kg/mm。
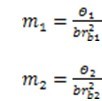
式中:b——齒寬,mm,這里應取各自的實際尺寸;
rb1、rb2——小輪及大輪基圓半徑,mm;
Θ1、Θ2——小輪及大輪的轉動慣量,kg,mm2。
對一般外嚙合傳動,齒輪副的誘導質量可近似按下式計算:
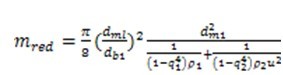
………….………………………..(26)
式中:ρ——材料密度,kg/mm3;
db——基圓直徑,mm;
dm——平均直徑,mm,dm=1/2(dn+df);

(對整體結構的齒輪,q=0);
Di——輪緣內(nèi)腔直徑,mm。
式(26)各代號的腳標1,2分別表示小輪和大輪。
上述各直徑的含義參見圖1。
圖1 齒輪各直徑
對于行星傳動和其他較特殊的齒輪,如小齒輪的平均直徑接近其軸徑,兩剛性聯(lián)接的同軸齒輪,兩個小輪驅動一個大輪等,其誘導質量可分別按表3和表4的分式近似計算。
表 3 行星傳動齒輪的誘導質量mred
齒輪組合 |
mred計算公式或提示 |
備注 |
太陽輪(S)-行星輪(P) |
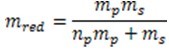 (27) |
np——輪系的行星輪數(shù);
ms,mp——太陽輪,行星輪的當量質量,可用式(24)及(25)計算 |
行星輪(P)-固定內(nèi)齒圈 |
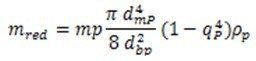 (28) |
把內(nèi)齒圈質量視為無窮大處理。
ρp——行星輪材料密度;
dm,db,q定義及計算參見式(26)說明及圖1 |
行星輪(P)-轉動內(nèi)齒圈 |
mred按式(26)計算,有若干個行星輪時可按單個行星輪分別計算 |
內(nèi)齒圈的當量質量可當作外齒輪處理 |
表4 較特殊結構型式的齒輪的誘導質量mred
齒輪結構型式 |
計 算 公 式 或 提 示 |
備注 |
1 |
小輪的平均直徑與軸頸相近 |
采用一般的計算公式,見式(26)。
因為結構引起的小輪當量質量增大和扭轉剛度增大(使實際嚙合剛度cy增大)對計算臨界轉速nE1的影響大體上相互抵消 |
|
2 |
兩剛性聯(lián)接的同軸齒輪 |
較大的齒輪質量必須計人,而較小的齒輪質量可以略去 |
若兩個齒輪直徑無顯著差別時,一起計入 |
3 |
兩個小輪驅動一個大輪 |
可分別按小輪1-大輪
小輪2-大輪
兩個獨立齒輪副分別計算 |
此時的大輪質量總是比小輪質量大得多 |
4 |
中間輪 |
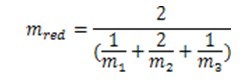 (29)
等效剛度
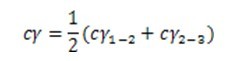 (30) |
m1,m2,m3為主動輪、中間輪、從動輪的當量質量;
cy1-2——主動輪、中間輪嚙合剛度;
cy2-3——中間輪、從動輪嚙合剛度 |
6.2.1.2 KV的計算式
臨界轉速比N對齒輪裝置的動載系數(shù)有著極其重要的影響,N=1時,運行轉速n等于臨界轉速,此時KV達最大值。在不同的N值區(qū)間,即不同的運行轉速區(qū)間,嚙合振動對KV的影響是不同的。考慮到振動模型的簡化和次要影響因素的忽略而帶來的計算結果與實際情況的偏差,將運行轉速N值劃分為4個區(qū)間,其相應的KV計算公式見表5。
表5 運行轉速區(qū)間及其動載系數(shù)KV的計算公式
運行轉速區(qū)間 |
臨界轉速比N |
對運行的齒輪裝置的要求 |
KV計算公式 |
備注 |
亞臨界區(qū) |
N≤NSNS |
多數(shù)通用齒輪在此區(qū)工作 |
KV=NK+1=N(CV1Bp+CV2Bf+CV3BK)+1 (31) |
在N=1/2或2/3時可能出現(xiàn)共振現(xiàn)象,KV大大超過計算值,直齒輪尤甚。此時應修改設計,在N=1/4或1/5時共振影響很小 |
主共振區(qū) |
NS<N≤1.5 |
一般精度不高的齒輪(尤其是未修緣的直齒輪)不宜在此區(qū)運行。εy>2的高精度斜齒輪可在此區(qū)工作 |
KV=CV1Bp+CV2Bf+CV4BK+1 (32) |
在此區(qū)內(nèi)KV受阻尼影響術大,實際動載與按式(32)計算所得值相差可達40%,尤其是對未修緣的直齒輪 |
過渡區(qū) |
1.15<N<1.5 |
|
 (33) |
KV(N=1.5)按式(34)計算。
KV(N=1.5)按式(32)計算 |
超臨界區(qū) |
N≥1.5 |
絕大多數(shù)透平齒輪及其他高速齒輪在此區(qū)工作 |
KV=CV5Bp+CV6Bf+CV7 (34) |
1.可能在N=2或3時出現(xiàn)共振,但影響不大。
2.當軸齒輪系統(tǒng)的橫向振動固有頻率與運行的嚙合頻率接近或相等時,實際動載與按式(34)計算所得值可相差100%,應避免此情況 |
注:
1 表中各式均每一齒輪副按單級傳動處理,略去多級傳動的其他各級的影響。非剛性聯(lián)結的同軸齒輪,可以這樣簡化,否則應按表4中第二類型情況處理。
2 亞臨界區(qū)中當(F tK A)/b<100N/mm時,N S=0.5+  ;其他情況時,N S=0.85。 |
表5各式中:Cv1——考慮齒距偏差的影響系數(shù);
Cv2——考慮齒形誤差的影響系數(shù);
Cv3——考慮嚙合剛度周期變化的影響系數(shù);
Cv4——考慮嚙合剛度周期性變化引起齒輪副扭轉共振的影響系數(shù);
Cv5——在超臨界區(qū)內(nèi)考慮齒距偏差的影響系數(shù);
Cv6——在超臨界區(qū)內(nèi)考慮齒形誤差的影響系數(shù);
Cv7——考慮因嚙合剛度的變動,在恒速運行時與輪齒彎曲變形產(chǎn)生的分力有關的系數(shù)。
上述Cv1,…Cv7的值可按表6中相應公式計算或由圖查取。
表6 CV系數(shù)值
總重合度
系數(shù)代號 |
1<εγ≤2 |
εγ>2 |
CV1 |
0.32 |
0.32 |
CV2 |
0.34 |
|
CV3 |
0.23 |
|
CV4 |
0.90 |
|
CV5 |
0.47 |
0.47 |
CV6 |
0.47 |
|
總重合度
系數(shù)代號 |
1<εγ≤1.5 |
1.5<εγ≤2.5 |
εγ>2.5 |
CV7 |
0.75 |
0.125sin〔π(εγ-2)〕+0.875 (41) |
1.0 |
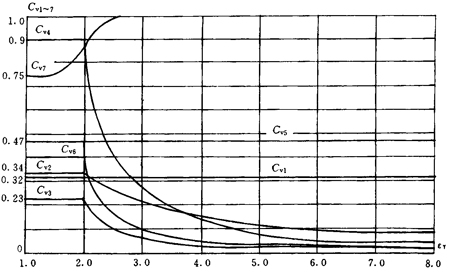
圖2 系數(shù)C
V1,…,C
V7的數(shù)值(相應公式見表6)
Bp、Bt、Bk——分別考慮齒距偏差、齒形偏差和輪齒修緣對動載荷影響的無量綱參數(shù)。
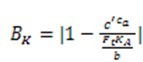
(對于齒輪精度低于5級者,應取B
K=1)…………………………..(44)
式中:Ft,FA——定義同前;
b——一對齒輪的較小齒寬,mm;
c′——單對齒剛度,N/(mm·μm),見6.5;
Ca——設計修復量,μm,沿齒廓法線方向計量。對無修緣齒輪,可用由跑合產(chǎn)生的齒頂磨合量Cay(μm)值代替。Cay可按下述公式計算。
當大、小輪材料相同時:

…………………………..(45)
當大、小輪材料不同時:
Cay=0.5(Cay1+ Cay2) …………………………..(46)
Cay1 ,Cay2分別按式(45)計算。
fpbeff,ffeff——分別為有效基節(jié)偏差和有效齒形公差,μm,與相應的跑合量Tp,Yf有關。
fpbeff =fpb-yp …………………………..(47)
ffeff =ff-yf …………………………..(48)
如無yp ,yt的可靠數(shù)據(jù),可近似取
yp= yf = ya
ya可按6.4.3中表17的公式計算。
fpb,ft通常按大齒輪查取相應的基節(jié)極限偏差和齒形公差.
6.2.2 簡化方法
KV的簡化法基于經(jīng)驗數(shù)據(jù),主要考慮齒輪制造精度和節(jié)線速度的影響。根據(jù)經(jīng)驗,在圖3所示的曲線范圍內(nèi)沒有考慮共振區(qū)的影響。本方法尤其適用于缺乏詳細資料的初步設計階段時KV的取值。
6.2.2.1 高精度齒輪
傳動精度系數(shù)C≤5的高精度齒輪,在良好的安裝和對中精度以及合適的潤滑條件下,KV值可按圖3取為1.0~1.1。C值根據(jù)6.2.2.2的條件按式(53)計算。
注:6~12為齒輪傳動精度系數(shù)
圖3 動載系數(shù)KV
6.2.2.2 其他齒輪
其他齒輪在符合下述條件時,KV值可按圖3查取或由式(50)計算。適用的條件是:
a)法向模數(shù)mn=1.25~50mm;
b)齒數(shù)z=6~1200(當mn>8.33mm時,用 取代1200);
c)傳動精度系數(shù)C=6~12,C的計算見式(53);
d)齒輪節(jié)線速度v不超過vmax
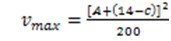
………………………..(49)
A與C的計算分別見式(51)和式(53)
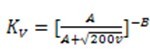
………………………..(50)
式中:
A=50+56(1.0-B)……………………………………(51)
B=0.25(c-5.0)0.667……………………………………(52)
C=-0.504 8ln(Z)-1.144ln(mn)+2.852ln(fpt)+3.32………………………(53)
式(53)計算的C值應作圓整,C=6~12;
z——大、小輪中計算得C值大者的齒數(shù);
mn——法向模數(shù)的值;
fpt——大、小輪中最大的單個齒距偏差的值。
6.3 齒向載荷分布系數(shù)KHβ,KFβ
6.3.1 KHβ的定義及影響因素
齒向載荷分布系數(shù)KHβ是考慮沿齒寬方向載荷分布不均勻對齒面接觸應力影響的系數(shù),其定義為:
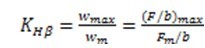
………………………..(54)
式中:ωmax——單位齒寬最大載荷,N/mm;
ωm——單位齒寬平均載荷,N/mm;
Fm——分度圓上平均計算切向力,N;Fm=FtKAKV。
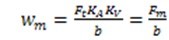
……………………..…..(55)
式中:b——齒寬,mm;對人字齒輪或雙斜齒輪,應取兩個斜齒輪寬度之和。影響齒向載荷分布的主要因素有:
a)齒輪副的接觸精度(GB 10095–88 第Ⅲ公差組精度),它主要取決于齒輪加工誤差、箱體鏜孔偏差、軸承的間隙和誤差、大小輪軸的平行度、跑合情況等;
b)輪齒嚙合剛度、齒輪的尺寸結構及支承型式及輪緣、軸、箱體及機座的剛度;
c)輪齒、軸、軸承的變形,熱膨脹和熱變形(這對高速寬齒輪尤其重要);
d)切向、軸向載荷及軸上的附加載荷(例如帶或鏈傳動);
e)設計中有無元件變形補償措施(例如齒向修形)。
由于影響因素眾多,確切的載荷分布系數(shù)應通過實際的精密測量和全面分析已知的各影響因素的量值綜合確定。這時,要論證應用方法的精確度和可靠性,并明確其前提條件。這種方法特別適用于調質小齒輪寬徑比b/d>1.5或硬齒面小齒輪b/d>1.2的重要齒輪裝置的校核計算。
各影響因素引起輪齒沿齒寬的綜合變形、位移和制造誤差的合成量稱初始嚙合齒向誤差(跑合前輪齒嚙合齒向誤差)以表示Fβx表示。它是決定齒向載荷分布系數(shù)的重要數(shù)據(jù)。在通過實測或綜合的精確計算得到初始嚙合齒向誤差Fβx時,可按式(56)至式(60)求得齒向載荷分布系數(shù)KHβ值。
當按上述方法得到的嚙合齒向誤差由齒向修形補償?shù)母呔三X輪副,在給定的運行條件下,其齒向載荷接近均勻分布,KHβ接近于1。
在無法按上述方法確定KHβ時,可按本標準提供的下述兩種方法——一般方法或簡化方法近似計算齒向載荷分布系數(shù)。
6.3.2 KHβ計算的一般方法
KHβ計算的一般方法適用條件列于6.3.2.1,計算公式按6.3.2.2。對于符合6.3.2.7中條件的一些典型結構齒輪裝置,如單對齒輪、軋機齒、簡單行星齒輪,其可KHβ按6.3.2.7所列公式計算。
6.3.2.1 基本假定和適用范圍
a)沿齒寬將輪齒視為具有嚙合剛度CY的彈性體,載荷和變形都呈線性分布(參見圖4);
b)軸齒輪的扭轉變形按載荷 沿齒寬均布計算,彎曲變形按載荷集中作用于齒寬中點計算,沒有其他額外的附加載荷;
c)箱體、軸承、大齒輪及其軸的剛度足夠大,其變形可忽略;
d)等直徑軸或階梯軸, dsh為與實際軸產(chǎn)生同樣彎曲變形量的當量軸徑;
e)軸和小齒輪的材料都為鋼;小齒輪軸可以是實心軸或空心軸(其內(nèi)徑應﹤0.5dsh)齒輪的結構支承形式見圖5,偏心距s/l≤0.3。
6.3.2.2 KHβ的計算公式
KHβ可用式(57)或式(59)計算
a) 當
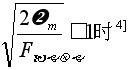
b
ca1/b=
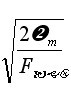
……………………..…………..(56)
K
Hβ=2(b/b
ca1)=

…………………………………(57)
b)
b
ca1/b=0.5+

…………………………………….(58)
采用說明:
4]ISO 6336原判別式為bca1/b在設計時為未知,故改用此判別式。
K
Hβ=
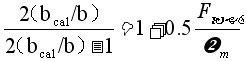
......................(59)
上述各式中:bca1——計算齒寬,見圖4;
Cy——輪齒嚙合剛度,見6.5;

—跑合后嚙合齒向誤差,UM;
ωm——計算見式(55)。

=

-yβ=

…………………………………………(60)
式中:

—初始嚙合齒向誤差,UM,見6.3.2.3;
yβ——齒向跑合量,UM,見6.3.2.6;
Xβ——齒向跑合系數(shù),見6.3.2.6.
當KHβ>1.5時,通常應采取措施降低KHβ值。
K’ |
圖號 |
結構示圖 |
剛性 |
非剛性 |
0.48 |
0.8 |
a) |
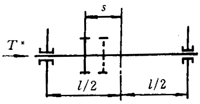 s/l<0.3 |
-0.48 |
-0.8 |
b) |
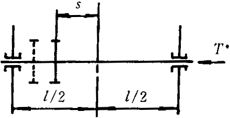 s/l<0.3 |
1.33 |
1.33 |
c) |
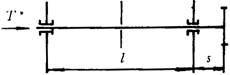 s/l<0.5 |
-0.36 |
-0.6 |
d) |
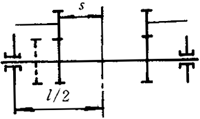 s/l<0.3 |
-0.6 |
-1.0 |
e) |
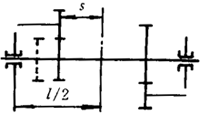 s/l<0.3 |
注
1 對人字齒輪或雙斜齒輪,圖中實、虛線各代表半邊斜齒輪中點的位置,S按用實線表示的變形大的半邊斜齒輪的位置計算,b取單個斜齒輪寬度。
2 圖中,d1/dsh ≥1.15為剛性軸,d1/dsh <1.15為非剛性軸。通常采用鍵聯(lián)接的套裝齒輪都屬非剛性軸。
3 齒輪位于軸承跨距中心時(S≈0),最好按6.3.2.7的公式計算。
4 當采用圖5以外的結構布置型式或s/l超過圖5規(guī)定的范圍,或軸上作用有皮帶輪或鏈輪之類的附加載荷時,推薦進一步的分析。
圖5 小齒輪結構系數(shù)K’
6.3.2.3初始嚙合向誤差KHβ
可據(jù)KHβ可據(jù)不同情況分別按式(61)~(63)計算。
a) 在載荷作用下沒達到全齒寬接觸或未能驗證有良好的接觸長度和位置時
=1.33fah+fma; 
≥F
βxmin………………………………………………(61)
b) 當已證實達到所希望的接觸斑點時(例如彩齒向修形或裝配時調整、對研、部分加載跑合、精確計算鼓形量或齒端修薄量等方法,使彈性變形和制造誤差相互補償)
=|1.33fah-
fma; 
≥F
βxmin………………………………………(62)
5]
c) 在載荷作用下達到理想的接觸斑點時

=F
βxmin………………………………………(63)
上述各式中:Fβxmin=max{(0.005mm·um/N)ωm,0.5Fβ}……………………………(64)
即Fβxmin取0.005ωmt 0.5 Fβ二者中之大值。Um;
fsh——綜合變形產(chǎn)生的嚙合齒向誤差分量,Um,見6.3.2.4;
fma——制造、安裝誤差產(chǎn)生的嚙合齒向誤差分量,Um,見6.3.2.5;
Fβ——齒向誤差,um;
Fβ6——GB10095-88的6級精度的齒向公差Fβ,um.
6.3.2.4 綜合變形產(chǎn)生的嚙合齒向誤差分量fsh
fsh——是考慮小齒輪和小齒輪軸的彎曲和扭轉變形產(chǎn)生的嚙合齒合誤差。
當 fsh無法實測或精確計算時,要按下式確定:
fsh=ωmfsho=(Fm/b)fsho………………………………………………(65)
式中fsh——載荷作用下的的嚙合齒向誤差,um;
fsho——單位載荷作用下的嚙合齒向誤差,um·mm/N;可按表7中的公式計算。
表7 fsho計算公式
齒輪型式 |
fsho計算公式 |
一般齒輪 |
0.023y (66) |
齒端修薄的齒輪 |
0.016y (67) |
修形或鼓形修整的齒輪 |
0.012y (68) |
表中:y——小齒輪結構尺寸系數(shù),可根據(jù)圖5先取系數(shù)K’值后,按表8中的公式計算。
表8 小齒輪結構尺寸系數(shù)y
齒輪型式 |
Y的計算
公式 |
B# |
功率不分流 |
功率分流,通過該對齒輪K%的功率 |
直齒輪及
單斜齒輪 |
|
B#=1 |
B#=1+2(100-k)/k |
人字齒輪或
雙斜齒輪 |
|
B#=1.5 |
B#=0.5+(200-k)/k |
注:l——軸承跨距,mm; s——小輪齒寬中點至軸承跨距中的距離,mm;d1——小輪分度圓直徑,mm;dsh——小輪軸彎曲變形當量直徑,mm;k’——結構系數(shù),見圖5;bB——單斜齒輪寬度,mm. |
采用說明:
5] 式(62)是ISO6336新增的,因含有|1.33fsh-fβ6|項,使用時需加限制條件(如精度及b/d值),否則將出現(xiàn)明顯不合理的結果。
6.3.2.5 制造、安裝誤差產(chǎn)生的嚙合齒向誤差分量fma
fma的大小取決于齒輪副加工的齒向誤差與軸線間平行度的組合(彼此疊加或補償)以及是否進行裝配調整。
如無實測數(shù)據(jù), fma可按表9中的方法之一確定。
表9fma計算公式(um)
類別 |
確定方法或公式 |
粗略數(shù)值 |
某些高精度的高速齒輪 |
fma=0 |
一般工業(yè)齒輪 |
fma=15μm |
給定精度等級 |
裝配時無檢驗調整 |
fma=1.0Fβ |
裝配時進行檢驗調整(對研,輕載跑合,調整軸承,螺旋線修形,鼓形齒等) |
fma=0.5Fβ |
齒端修薄 |
fma=0.7Fβ |
給定空載下接觸斑點長度bco |
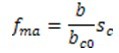 (71)
SC——涂色層厚度,一般為2~20μm,計算時可取
SC=6μm
如按最小接觸斑點長度bcomin計算
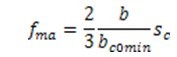 (72)
如測得最長和最短的接觸點長度
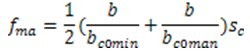 (73)
|
6.3.2.6 齒向跑合量yβ,跑合系數(shù)Xβ
齒向跑合量yβ是考慮跑合后使嚙合齒向誤差減小的量,um; Xβ是表示跑合嚙合齒向誤差Fβy的比例數(shù)據(jù),yβ,Xβ可用表10中各式計算。
表10 yβ、Xβ 計算公式
齒輪材料 |
齒向跑合量yβ,um,跑合系數(shù)Xβ |
適用范圍及限制條件 |
結構鋼、調質鋼、珠光體或貝氏體球墨鑄鐵 |
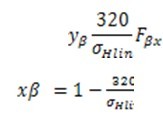 (74) |
V>10m/s時,
yβ≤12800/σHlim FβX≤40μm; ≤12
5<v≤10m/s時,
yβ≤25600/σHlim
FβX≤80μm;
v≤5m/s時,
yβ無限制 |
灰鑄鐵、鐵體球墨鑄鐵 |
yβ=0.55FβX
xβ=0.45 (75) |
V>10m/s時,
yβ≤22μm, FβX≤40μm; ≤12
5<v≤10m/s時,
yβ≤45μm, FβX≤80μm;
v≤5m/s時,
yβ無限制 |
滲碳淬火鋼、表面硬化鋼、氮化鋼、
氮碳共滲鋼、表面硬化球墨鑄鐵 |
yβ=0.15FβX
xβ=0.85 (76) |
yβ≤6um. FβX≤40um |
注
1σhlim——齒輪接觸疲勞限值,N/mm2,見8.1.2
2 當大小齒輪材料不同時,yβ=(yβ1+ yβ2)/2,Xβ=(Xβ7=+Xβ2)/2,式中下標1,2分別表示大、小齒輪。 |
6.3.2.7 典型結構齒輪的FβX
a)適用條件
1)沿齒寬將齒輪視為具有嚙合剛度cy的彈性體,載荷和變形均呈線性分布;
2)在載荷作用下接觸斑點布滿全齒寬,軸齒輪的扭轉和彎曲變形均按載荷沿齒寬均布計算,沒有其他額外的附加載荷;
3)小齒輪直徑和軸徑相近,軸齒輪為實心或空心軸(內(nèi)孔徑應<0.5dsh),對稱布置在兩軸承之間(s/l≈0);非對稱布置時,應把估算出的附加彎曲變形量加到fma上;
4)箱體、軸承、大齒輪及其軸的剛度足夠大,其變形可忽略。
符合上述條件的單對齒輪、軋機齒輪和簡單行星傳動可按下述b)~d)中的公式計算KHβ.
b) 單對齒輪
符合a)中條件的單對齒輪,可按表11中的公式計算KHβ.
表11 單對齒輪的KHβ計算公式
齒輪類型 |
修形情況 |
KHβ計算公式 |
直齒輪、斜齒輪 |
不修形 |
|
部分修形 |
|
完全修形 |
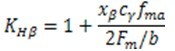 且K Hβ≥1.05 |
人字齒輪或雙斜齒輪 |
不修形 |
|
完全修形 |
 且K Hβ≥1.05 |
注
1 本表各公式適用于全部轉矩從軸的一端輸入的情況,如同時從軸的兩端輸入或雙斜齒輪人兩半邊斜齒輪的中間輸入,則應作更詳細的分析。
2 部分修形指只補償扭轉變形的螺旋線修形;完全修形指同時可補償彎曲、扭轉變形的螺旋線修形。
3 B——包括空刀槽在內(nèi)的雙斜齒全齒寬,mm;bB——單斜齒輪寬度,mm.對因結構要求而超過一般工藝需要的大齒槽寬度的雙斜齒輪,應采用一般方法計算。 |
c) 軋機齒輪
軋機齒輪機座采用一對軸齒輪,u=1,功率分流,被動齒輪傳遞k%的轉矩、另外(100-K)%有轉矩由主動齒輪的軸端輸出,兩齒輪皆對稱布置在兩端的軸承之間,其KHβ值可按表12中公式計算。
表12 軋機齒輪的KHβ計算公式
是否修形 |
齒輪類型 |
KHβ計算公式 |
不修形 |
直齒輪、
斜齒輪 |
 (82) |
雙斜齒輪或
人字齒輪 |
 (83) |
完全修形 |
直齒輪、
斜齒輪 |
按式(79) |
雙斜齒輪或
人字齒輪 |
按式(81) |
注
1 如按式(83)計算的KHβ>2,應核查設計,最好用更精確的方法重新計算。
2 B為包括空刀槽在內(nèi)的雙斜齒寬度,mm;bB為單斜齒輪寬度,mm. |
d) 簡單行星傳動齒輪
符合項a)中條件的行星傳動中的各齒輪副:太陽輪(S)/行星輪(P)、內(nèi)齒輪(H)/行星輪,其KHβ可按表13中的公式計算。計算時應取
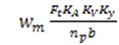
……………………………………….(84)
式中:ωm——單位齒寬平均載荷,N/mm;
Ky——不均載系數(shù);
Np——行星輪個數(shù)。
表13 行星傳動齒輪的KHβ計算公式
|
齒輪副 |
軸承型式 |
修形情況 |
KHβ計算公式 |
直齒輪、單斜齒輪 |
太陽輪
(S)
|
行星輪
(P) |
Ⅰ |
不修形 |
 (85) |
修形(僅補償
扭轉變形) |
按式(79) |
Ⅱ |
不修形 |
 (86) |
完全修形(彎曲和扭轉變形完全補償) |
按式(79) |
內(nèi)齒輪
(H)
|
行星輪
(P) |
Ⅰ |
修形或不修形 |
按式(79) |
Ⅱ |
不修形 |
 (87) |
修形(僅補償彎曲變形) |
按式(79) |
人字齒輪或雙斜齒輪 |
太陽輪
(S)
|
行星輪
(P) |
Ⅰ
|
不修形 |
 (88) |
修形(僅補償彎曲變形) |
按式(81) |
Ⅱ |
不修形 |
 (89) |
完全修形(彎曲和扭轉變形完全補償) |
按式(81) |
內(nèi)齒輪
(H)
|
行星輪
(P) |
Ⅰ |
修形或不修形 |
按式(81) |
Ⅱ |
不修形 |
 (90) |
修形(僅補償彎曲變形) |
按式(81) |
注
1 Ⅰ,Ⅱ表示行星輪及其軸承在行星架上的安裝型式:Ⅰ——軸承裝在行星輪上,轉軸剛性固定在行星架上;Ⅱ——行星輪兩端帶軸頸的軸齒輪,軸承裝在轉架上。
2 ds——太陽輪分度圓直徑,mmdp——行星輪分度圓直徑,mm;;lp——行星輪軸承跨距,mm;
B為包括空刀槽在內(nèi)的雙斜齒寬度,mm;bB為單斜齒輪寬度,mm. |
6.3.3 KHβ計算的簡化方法
6.3.3.1 適用范圍
a) 中等或較重載荷工況:對調質齒輪,單位齒寬載荷Fm/b為400~1000N/mm;對硬齒面齒輪,F(xiàn)m/b為800~1500N/mm。
b) 剛性結構和剛性支承,受載時兩軸承變形較小可忽略:齒寬偏置度s/l較小,符合表14、表15限定范圍。
c) 齒寬b為50~400mm,齒寬與齒高比b/h為3~12,小齒輪寬徑比b/d1對調質的應小于2.0,對硬齒面的應小于1.5.
d) 輪齒嚙合剛度cy為15~25N/(mm·um).
e) 齒輪制造精度對調質齒輪為5~8級,對硬齒面齒輪為5~6級;滿載時齒寬全長或接近全長接觸(一般情況下未經(jīng)齒向修形)。
f) 礦物油潤滑。
6.3.3.2 計算公式
齒輪第Ⅲ公差組精度為5~8級(硬齒面為5~6級)及相應的結構布局限制條件的KHβ簡化計算公式見表14或表15。
表14 調質齒輪KHβ的簡化計算公式
表15 硬齒面齒輪KHβ的簡化計算公式
6.3.4 KFβ的計算公式
齒向載荷分布系數(shù)KFβ是考慮沿齒寬載荷分布對齒根彎曲應力的影響。對于所有的實際應用范圍,KFβ可按下式計算:
KFβ=(KHβ)N…………………………………………….(139)
式中:KHβ——接觸強度計算的齒向載荷分布系數(shù),見6.3.2或6.3.3;
N——冪指數(shù)。
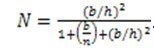
…………………………….(140)
式中:b——齒寬,mm,對人字齒或雙斜齒齒輪,用單個斜齒輪的齒寬;
H——齒高,mm.
b/h應取大小齒輪中的小值。
圖6給了按式(139)、(140)確定的近似解。
圖6 彎曲強度計算的齒向載荷分布系數(shù)KFβ
齒間載荷分配系數(shù)KHa,KFa
齒間載荷分配系數(shù)是考慮同時嚙合的各對輪齒間載荷分配不均勻影響的系數(shù)。齒間載荷分配系數(shù)的定義為:在無任何動載荷的情況下,一對齒輪在嚙合區(qū)內(nèi)輪齒上的最大載荷與相同的一對精確齒輪輪齒的相應最大載荷之比。
影響齒間載荷分配系數(shù)的主要因素有:
a) 受載后輪齒變形;
b) 輪齒制造誤差,特別是基節(jié)偏差;
c) 齒廓修形;
d) 跑合效果。
齒間載荷分配系數(shù)如能通過精密實測或對所有影響因素的精確分析得到,則應優(yōu)先采用;但此時應對其測量或分析方法的精度和可靠性進行論證。在一般情況下,可按下述方法確定KHa,KFa。
6.4.1 一般方法
齒間載荷分配系數(shù)一般可按下式確定:
當總重合度εy≤2時

…………………………….(141)
當總重合度εy>2時
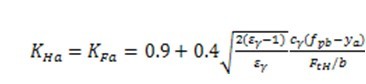
…………………………….(142)
按式(141)或(142)計算時
若

,則取;若

;K
Ha<1.0,則取K
Ha=1.0
若

,則。蝗

;K
Fa<1.0,則取K
Fa=1.0
但對于斜齒輪,如計算得的KHa值過大,則應調整設計參數(shù),使得KHa及KFa不大于εao同時,式(141)和(142)僅適用于齒輪基節(jié)偏差在圓周方向呈正常分布的情況。
上述各式中:εγ——總重合度;
εγ=εa+εβ……………………………………….(143)
cγ——嚙合剛度,見6.5;
fpb——基節(jié)極限偏差,通常以大輪的基節(jié)極限偏差計算;當有適宜的修緣時, 按此值的一半計算;
Ya——齒廓跑合量,見6.4.3;
Zε,Yε——接觸強度和彎曲強度的重合度系數(shù),分別見7.1.3和7.2.3;
FtH=FtKAKVKHβ………………………………………(144)
FtH——計算FHa時的切向力,N;
Ft,KA,KV,KHβ——見第5章6.1-6.3。